- Borza D55 Developer Community Driver Download Windows 7
- Norza D55 Developer Community Driver Download Windows 7
Updating Drivers since 1998! Fast Driver Downloads for all of your PCs — Notebooks and Desktops. Access to over 3,100 GB of driver downloads. Drivers for Windows 10, 8.1, 8, 7, Windows Vista, Windows XP, and hard-to-find drivers. Printer Drivers, Audio Drivers, Video Drivers, and hundreds of other types. Studio Driver X NVIDIA does extensive testing which focuses on the top creative applications and ensures the highest levels of performance, stability, and functionality are provided. Join an ever-growing community of car lovers to talk about everything Forza! Looking for driving tips? You love cars and want to talk cars, the Forza community is full of people like you that love everything with four wheels and a motor. Get tuning and painting tips and learn about the latest Forza related contests. Join the discussion in the.
If your RepRap only uses stepper motors, like most of the top-rated RepRaps in the Comparison of Electronics, and you run them at low speed and low acceleration so they don't skip steps, you don't need this or any other encoder.
However, if you want to run faster than possible with a stepper motor, read on.
As of 2014, this is the most recent magnetic rotary encoder designed for RepRap.As of 2014, this is the best encoder of any kind designed for RepRap -- see RepRapServo 1 0 for an overview of various kinds of encoders.
I am a part of both, Generation 2 Electronics and Generation 3 Electronics Systems.
This is an advanced, surface mount board. It requires steady hands and patience to solder.
Don't worry though, You Can Do It!
The Magnetic Rotary Encoder board is based around the Austria MicrosystemsAS5040 chip. This chip allows you to sense the rotational position of a magnet. Sounds boring, right? Wrong! When you combine this chip with a motor, a motor driver, and an Arduino it allows you to create a servo motor of unlimited size and rotation. You can measure the rotation of the motor and control it so that it goes to the position you desire. Or, in the case of our extruder, you can measure the speed of the motor and have it rotate at exactly the speed you desire, regardless of the load on the motor.
- You'll need a soldering toolkit to do most of this.
- Read our Electronics Fabrication Guide if you're new.
- 2Files
- 3Interface
- 4Build It
- 4.2Components
- 5Mount It
- 6Use It
Get It!
There are currently no known kit sellers. For help on collecting the parts, see below.
Files
You can download the electronics files from Sourceforge.
This file contains the following:
- GERBER files for getting it manufactured
- PDF files of the schematic, copper layers, and silkscreen
- Eagle source files for modification
- 3D rendered image as well as POVRay scene file
- exerciser code to test your board.
Schematic
Interface
The AS5040 provides many different ways of getting the position data from the chip. Each one has its advantages and disadvantages, so feel free to use the one best suited to your needs.
Pinout
Pin | Name | Function |
1 | PWM | A PWM output signal, where the width of the pulse (1 usec to 1023 usec wide) is based upon the position of magnet (0-360 degrees) |
2 | ANALOG | An analog output signal from 0-5v signifying the position of the magnet (0-360 degrees) |
3 | SELECT | The AS5040 provides a digital output using SSI, this is the select (or latch) pin. |
4 | CLOCK | The AS5040 provides a digital output using SSI, this is the clock pin. |
5 | DATA | The AS5040 provides a digital output using SSI, this is the data (or MISO) pin. |
6 | INDEX | When the magnet is at the 0 degrees position, this pin is HIGH, otherwise LOW. This pin will pulse once per revolution |
7 | B | The AS5040 outputs quadrature signals. This pin is the Quadrature Phase B signal |
8 | A | The AS5040 outputs quadrature signals. This pin is the Quadrature Phase A signal |
9 | GND | This is the ground pin. Connect this to ground on your Arduino. |
10 | 5V | This is the 5V input pin. Connect this to 5v on your Arduino. |
LEDS
LED | Meaning |
MAG+ | This is the Magnetic Field Increasing LED. If the magnetic field strength is increasing, this LED will light up. |
MAG- | This is the Magnetic Field Decreasing LED. If the magnetic field strength is decreasing, this LED will light up. |
QUAD_A | This LED is directly wired to Quadrature Phase A, it gives you a direct view of the chip activity. |
QUAD_B | This LED is directly wired to Quadrature Phase B, it gives you a direct view of the chip activity. |
INDEX | This LED is directly wired to the Index pin, it will flash once per revolution. |
PWM | This LED is wired to the PWM pin, along with a capacitor. Its brightness will vary according to the position of the magnet. |
Sagem drivers for windows 7. If both MAG+ and MAG- are on, it means your magnet is Out of Range. If they sporadically light during magnet rotation, it means your magnet alignment is slightly out of range. Adjust it accordingly until they do not light during normal use. Use these LEDs to align your magnet properly.
Build It
Circuit Board
Currently, there are no known vendors of this PCB, so you have to make your own or order custom made ones from a prototype PCB manufacturer. The image shows the professionally manufactured PCB once sold by the RepRap Research Foundation.
Components
Part | Name | Quantity | Type |
---|---|---|---|
PCB | Magnetic Rotary Encoder v1.0 PCB | 1 | pcb |
C1 | 100nF ceramic capacitor 1206 | 1 | component |
C2 - C5 | 1uF electrolytic capacitor D55 | 4 | component |
C6 | 10nF ceramic capacitor 1206 | 1 | component |
IC1 | AS5040 | 1 | component |
LED1 - LED6 | Green LED 1206 | 6 | component |
R1, R4, R6 - R9 | 560 ohm resistor 1206 | 6 | component |
R2, R3, R5 | 4.7k ohm resistor 1206 | 3 | component |
10 pin IDC header | 1 | component | |
10 pin IDC connector | 1 | component | |
10 pin ribbon cable | 36 | wire | |
AS5040 magnet | 1 | misc |
Soldering Instructions

This is a mostly surface mount component board, so the techniques will be a bit different than usual. In addition to your standard soldering toolkit, you will also need the following:
- a soldering iron with a good, small tip
- some tweezers, or small needle nose pliers
- some thin solder (0.025' diameter or smaller)
- a flux pen, flux paste, or other flux dispensing device
- some solder wick
- a magnifying glass
Before you start, you may want to watch this video on Surface Mount Soldering and/or read the SparkFun tutorial.
10nF capacitor
The 10nF and 100nF capacitors themselves are not marked, so we have marked the 10nF capacitor with blue marker. If you mix them up, don't worry its okay.
The orientation on this capacitor does not matter.

The basic process goes like this:
- apply a small bit of solder to one of the raw pads to prep it
- pick up component with tweezers, and apply a small amount of flux to the ends
- position the component in place and heat one side with the iron (causing it to bond to the pad on that side)
- solder the other side to the other pad. if its sticking up a bit, solder it until the entire chip heats up and settles in.
- you may need to add more solder to either side to get a nice solid joint
100nF capacitor
Follow the directions above to solder the non-marked capacitor in.
The orientation on this capacitor does not matter.
560 Ohm Resistors
These resistors will all be marked '561'. The orientation does not matter, but it helps to solder them so the text is all facing the same way. Do as I say, not as I do ;)
Solder them with the same technique you used for the capacitors.
4.7K Ohm Resistors
These resistors will be marked '472'. Solder them in just as with the 560 ohm resistors.
LEDS
The LEDs are polarized, meaning you need to solder them in the correct orientation! They will have green dots towards one side of the package. These dots need to match the dots on the silkscreen. Be careful, since the orientation changes for the various LEDs. Always check and double check the orientation before you solder.
Other than that, you can solder them using the same technique you used above. Be careful not to heat them up too much, as you may damage them.
Borza D55 Developer Community Driver Download Windows 7
AS5040
This is the hardest part of the board. Take a quick break before you do it. Wipe the sweat from your brow, take a deep breath, and calm yourself.
1. 2. 3. 4. 5. Exhale.
Awesome, lets start. First off, the chip needs to be soldered in properly. There is a circle mark on the chip that corresponds to the mark on the silkscreen. Make sure they match up before you solder.
The basic soldering process goes like this:
- use flux on the legs of the chip and/or the board
- position the chip over the pads
- solder one corner of the chip to the corresponding pad
- solder the opposite corner of the chip to the corresponding pad
- solder the rest of the pins, ignoring solder bridges
- use the solder wick to remove any solder bridges
- profit!
If you're still confused, please watch this video. It will change your life. Maybe.
If all goes well, you'll have a nicely soldered chip. The rest is simple.
1uF Electrolytic Capacitors
These guys are the little tin-can looking things. They have polarity, so be sure to double check which way you are soldering them to the board. One side will have square corners, and the other will have beveled edges. Make sure you match these up with the silkscreen.
Once you understand how to place them, you'll want to prepare the surface for mounting just like you did with the other capacitors, resistors, and LEDs by applying a bit of solder to the empty pads. Then you simply solder the capacitor down one pad at a time. Yay!
IDC Header
This is where you will plug in the IDC cable to your board. Solder it so the center tab faces the center of the board. Just like it shows on the silkscreen!
This one is thru-hole and thus insanely easy compared to what you just did.
Insert IDC Connector
First, you must make an IDC cable. Next, insert it into the header. It is keyed, so it can only be inserted in one orientation. Yay!
Congratulations, you just soldered a fairly difficult board. Go have a frosty beverage of your choice to celebrate.
Mount It
GM3 Gear Motor
The Magnetic Rotary Encoder Board provides precise mounting holes to mount it to a GM3 Gearmotor. You'll need spacers that are 7/16' long to space the board far enough away.
Attach the Magnet
Norza D55 Developer Community Driver Download Windows 7
The first step is to mount the magnet on the GM3 gearmotor's non-output shaft. This is the shaft with one flat side, NOT the shaft with two flat sides. Get some super glue and put a dab on the shaft of the motor. Quickly place the magnet onto the shaft, being careful that the magnet is closely aligned with the motor shaft. It should be slightly inside the curve of the shaft. Press firmly for 10 seconds to allow the glue to bond. If you messed up, pry the magnet off and try again. It may take 2 applications of the superglue to get a good bond. Finally, clean off any gunk from the side and top of the magnet.
Mount the MRE Board
Using the M3 bolts, attach the MRE to the GM3 Motor using the spacers provided. The magnet should just barely enter the large drill hole beneath the chip. You can then mount the GM3 motor wherever you need it to be mounted. If you need more spacing, you can easily add a washer or two between the spacer and the motor.
Mounting on a Kysan DC Gearmotor
Mounting on a Makerbot Kysan DC Gearmotor:'Encoder Mount'
Other Uses
You can use the MRE board to measure rotation for many things, and we've provided 6 different mounting holes for you to use. The magnet can be positioned directly above or below the AS5040 chip, and we've provided a 6.1mm diameter hole that will help with aligning the magnet as well. Please refer to the AS5040 datasheet for more information on mounting tolerances.
Use It
Quadrature Output
Quadrature Encoding is very useful. It allows you to determine both position and rotation direction in a simple manner. Not only that, but it is incremental, which means that you can use quadrature encoding to record positions that are as large as you can store in your variable!!!
Not only that, but it only uses 2 pins. Rad.
Here is an Arduino program to read the position via quadrature encoding. Connect the pins as follows:
MRE Pin | Arduino Pin |
5V | 5V |
GND | GND |
QUAD_A | 2 |
QUAD_B | 3 |
Then, upload this code, and open your Serial Monitor at speed 19200.
Digital SSI Output
The AS5040 provides a digital output which is also very useful. It uses 3 pins, but provides some other useful features such as a checksum, and error flags to help you diagnose any potential errors. Additionally, it is possible to do some advanced things with the digital output, such as daisy chaining AS5040 chips to allow you to read multiple AS5040 chips with the same 3 pins, or allowing you to read them in parallel using 2 + N pins where N is the number of AS5040 chips to use.
It has some very useful potential.
Here is an Arduino program to read the position via the digital interface. Connect the pins as follows:
MRE Pin | Arduino Pin |
5V | 5V |
GND | GND |
SELECT | 4 |
CLOCK | 5 |
DATA | 6 |
Then, upload this code, and open your Serial Monitor at speed 19200.
Analog Output
By using a filter circuit, the AS5040 is capable of outputting an analog position value. Its not nearly as accurate as the Quadrature or Digital outputs, but it is useful in its own right.
Here is an Arduino program to read the position via analog. Connect the pins as follows:
MRE Pin | Arduino Pin |
5V | 5V |
GND | GND |
ANALOG | Analog 0 |
Then, upload this code, and open your Serial Monitor at speed 19200.
PWM Output
Coming soon. Anyone have a good idea on how to use this output?
Index Output
Coming soon. This one is pretty easy.
Similar Parts
- Is the MagServo significantly different from this Magnetic Rotary Encoder 1.0?
- the open-source OpenServo OpenEncoder seems surprisingly similar to this RepRap magnetic rotary encoder.
- 'AS5040 Breakout Board Assembly' seems surprisingly similar to this RepRap magnetic rotary encoder. The breakout board and magnets are available via Mad Scientist Hut: CNC and Robotic Sensors
- KMZ10 (A/B/C) is analog encoder (only analog output) - it is very cheap - 1$ and simple to interface with (just one differential amp)
- This Magnetic Rotary Encoder 1.0 can be seen in action in the Grass Roots Engineering 3D printer (Grass Roots Engineering: assembling the encoder board and Grass Roots Engineering 3D printer).
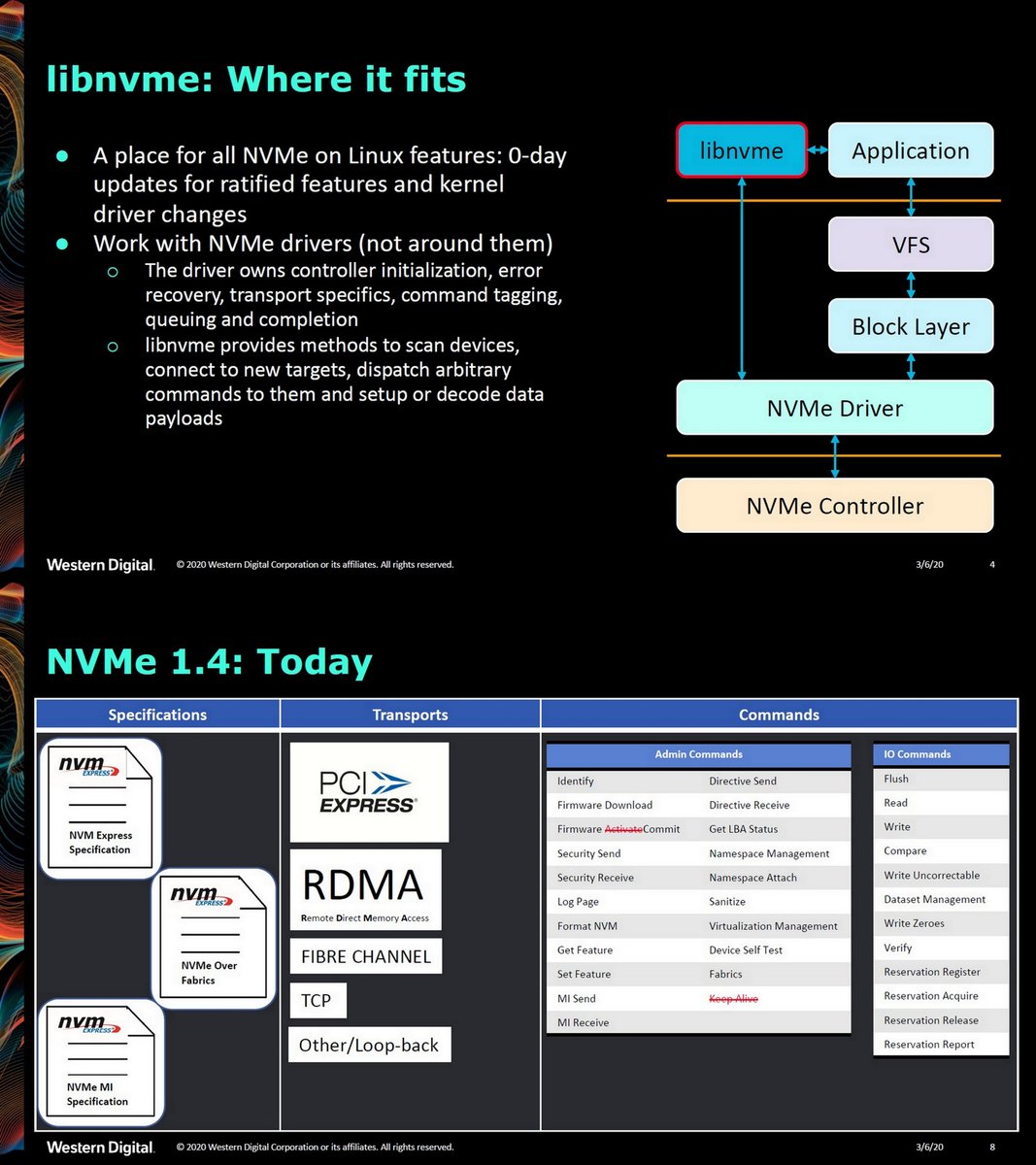
Quadro RTX 6000, Quadro RTX 5000, Quadro RTX 4000
Quadro GV100, Quadro GP100, Quadro P6000, Quadro P5200, Quadro P5000, Quadro P4000, Quadro P2000, Quadro P1000, Quadro P620, Quadro P600, Quadro P400, Quadro M6000 24GB, Quadro M6000, Quadro M5000, Quadro M4000, Quadro M2000, Quadro K6000, Quadro K5200, Quadro K5000, Quadro K4000, Quadro K4200, Quadro K2200, Quadro K2000, Quadro K2000D, Quadro K1200, Quadro K620, Quadro K600, Quadro K420, Quadro 410
Quadro P5200, Quadro P5000, Quadro P4200, Quadro P3200, Quadro P4000, Quadro P3000, Quadro P2000, Quadro P1000, Quadro P600, Quadro P500, Quadro M2200, Quadro M1200, Quadro M620, Quadro M520, Quadro M5500, Quadro M5000M, Quadro M4000M, Quadro M3000M, Quadro M2000M, Quadro M1000M, Quadro M600M, Quadro M500M, Quadro K5100M, Quadro K5000M, Quadro K4100M, Quadro K4000M, Quadro K3100M, Quadro K2200M, Quadro K2100M, Quadro K3000M, Quadro K2000M, Quadro K1100M, Quadro K1000M, Quadro K620M, Quadro K610M, Quadro K510M, Quadro K500M
Quadro P5000, Quadro P3000, Quadro M5000 SE, Quadro M3000 SE, Quadro K3100M
NVS 810, NVS 510
Quadro Sync II, Quadro Sync
NVS 810, NVS 510
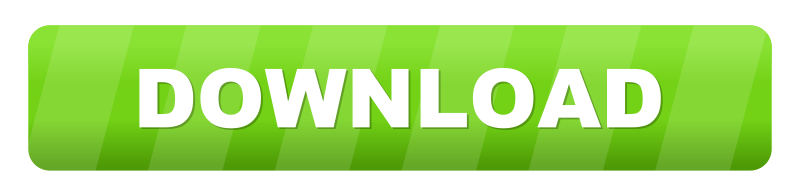